Prof. Dr. Christoph Hartl
Dr.-Ing.Institut für Produktion (IFP)
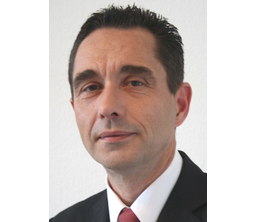
Campus Deutz
Betzdorfer Straße 2
50679 Köln
Raum ZN 7-6
Postanschrift
+49 221-8275-2550
christoph.hartl@th-koeln.de
Sprechstunden
Nach Vereinbarung
00.00 bis 00.00 Uhr
Campus Deutz, Betzdorfer Str. 2, Raum ZN 7-6
Lehrgebiete
- Fertigungsverfahren | Manufacturing Technology
Forschungsgebiete
-
Fertigungsverfahren: Prozessentwicklung, -optimierung und -analyse, Umformtechnik metallischer und polymerer Werkstoffe, Mikrotechnik, Fügetechnik, Werkzeuge und Maschinensysteme
-
Modellierung und Simulation: Lineare und nichtlineare FEM-Simulation, Machbarkeitsuntersuchungen zu Umformprozesse, thermisch-mechanisch-gekoppelte Analysen, Strukturberechung, Topologieoptimierung, Prozessmodellierung mit künstlichen neuronalen Netzwerken
-
Materialbearbeitung mit Lasern: Prozessentwicklung und -analysen, Mikro-Strukturierung, Schweißen,Löten, Schneiden, metallische und nichtmetallische WerkstoffeORCID
Projekte / Kooperationen
-
Public funded projects / Öffentlich geförderte Projekte:
-
hybrid+smartMore information
The hybrid+smart project aims to scale up and validate an innovative concept of smart and hybrid energy harvesting systems involving photovoltaics, thermoelectrics and intelligent sensor technology based on Internet of Things for the use as façade elements in integrated building envelope systems. The focus of the conducted work is on the implementation of manufacturing technologies that allow for cost-effective realisation in series production. In hybrid+smart, the Technische Hochschule Köln is working together with the Institute for Production Technology and Organisation gGmbH – IPTO on the development, testing and validation of this innovative smart and hybrid energy harvesting concept. In this context, a demonstrator is being built that prioritises manufacturing and assembly-orientated design and harmonised parameters for photovoltaics and thermoelectrics. Laboratory experiments and field tests are used to evaluate and validate the hybrid and smart manufacturing concept and to demonstrate the potential for increased efficiency. hybrid+smart is financed for the period from October 2024 to June 2025 by the iClimaBuilt consortium, which is funded by the European Union. The iClimaBuilt partners E2ARC, Eurecat, Fraunhofer ISE, Stratagem and TEGnology are actively supporting hybrid+smart with their pilot lines and services. -
Characterisation of joining techniques on hybrid solar systems
An important aspect in the context of the manufacture of hybrid systems consisting of photovoltaic modules and thermoelectric devices is the economic, reliable and durable connection of the thermoelectric components to the photovoltaic panels. This poses certain challenges, as different and partly difficult to join materials with different thermal expansion coefficients have to be joined and at the same time a low thermal resistance is required. As part of the project PolyCon, funded by the Deutsche Forschungsgemeinschaft DFG since December 2023, suitable joints are being characterised using the latest technologies in order to derive optimisation opportunities for connections with high thermal conductivity and durability. -
FAST and Nano-Enabled SMART Materials, Structures and Systems for Energy HarvestingFAST-SMART
FAST-SMART started in 2020 and is promoted for four years within the Horizon 2020 programme of the European Commission. The work of the 13 European research partners in the FAST-SMART project focuses on the scaling of new manufacturing processes for the large-scale production of nanostructured smart materials and their application in innovative systems for the recovery of energy, which is lost unused as dissipated energy in many technical systems. For this purpose, project partners are researching new strategies to shorten process chains for better economic efficiency and to improve necessary material properties while reducing rare elements. The TH Köln is implementing these materials designed in FAST-SMART and is, based on them, developing economic manufacturing strategies for the production of expanded photovoltaic systems that enable additional recovery of usually lost thermal energy. -
Finite Element Analysis of heat treatment induced bending distortion of cutting tools for medical technology
The geometry of surgical milling cutters is often characterized by a high ratio of length to diameter that increases the susceptibility to distortions in heat treatment processes. To reduce the probability of distortions, the manufacturing chain of these products has to be seen as a whole and analyses of possible sources have to consider each step that can contain possible causes of distortion. Objective of this project that started in 2018 is to analyze this manufacturing chain with the aid of finite element models and to work out measures for distortion reduction. The results of this study serve to support the project "Multivariate optimization of processes" at the University of Wuppertal, funded by the Federal Ministry of Education and Research. -
Ready-to-manufacture design of lightweight carrying devices for architectural building elements
With the support of the State of NRW and in cooperation with an architect from the Cologne-Bonn region this project started in 2015. Objective is the implementation of a patented idea dealing with flexible carrying devices for architectural building elements mounted in large heights. Focus of the work conducted by the TH Köln is on the lightweight design of the carrying devices with particular regard to durability and economic manufacture. Simulation methods based on FEA are used for design optimization. -
CPU-cooling system with energy recovery based on thermogenerators
Supported by the Federal Ministry for Economic Affairs and Eneregy since 2013 this project is working on the development of a fluid-based cooling system for computer processors. The basic strategy consists in the application of a new thermogenerator concept to recover the emitted heat of processors. Improved cooling efficiency and reduction in size and weight of required cooling devices are additional objectives of the conducted research work. The project partner angaris GmbH is resonsible for the new thermogenerator design which is aimed at reduced production costs. Besides the overall cooling system layout, the Cologne University of Applied Science is working on investigations into the application of micro-manufacturing technology for an economic series production of the required heat exchangers with micro-channel structure. -
POLYTUBES
The POLYTUBES project started in 2009 and was promoted for three years within the 7th Framework Programme of the European Commission. Overall objective was to develop a process chain and a corresponding micro-manufacturing platform for the manufacture of polymer-microtubes and tubular micro-components for innovative products concerning medical and non medical applications. With 16 European partners it created new markets for SMEs with innovative and economically competitive micro-products and micro-manufacturing equipment to meet the needs for a wide range of emerging applications. Within this project the Cologne University of Applied Sciences developed a machine system for micro-blow moulding of polymeric micro-components in mass production. Manufactured demonstrators for consumer goods show the full potential of this new production technology. -
MASMICRO
Launched in 1st July 2004, MASMICRO was an Integrated Project for the Integration of Manufacturing Systems for Mass-Manufacture of Miniature/Micro-Products, supported by the European Commission under the 6th Framework Programme. This four-year flagship micro-manufacturing project involved a consortium composed of 36 partners from 13 EU countries, including 18 industrial partners. The total budget of the project was over 21 million euros. As one of these partners the Cologne University of Applied Sciences developed successfully the fundamentals for processes and machine systems for the new forming technology “micro-hydroforming” under the direction of Prof. Dr. Christoph Hartl. Today, micro-hydroforming enables the cost-effective production of hollow shaped micro-components from metal materials.
Publikationen
-
Publication summary: https://orcid.org/0000-0003-3630-8739ORCID
-
Selected Publications:
-
Development, optimization, and testing of a hybrid solar panel concept with energy harvesting enhancementDOI
Pattath Saseendran, A.; Hartl, Ch.; Tian, Y.; Qin, Y., 2023, Hg.: Journal of Physics: Conference Series 2526 (2023) 012033
-
Laser Welding of Nitinol Thin Foils: Mechanical Properties and Microstructure Depending on Process ParametersDOI
Katrakova-Krüger, D.; Pegoraro; L.; Salmaso, L.; Hartl, Ch.; Schulz, I.; Weichert, S.; Steffen, R., Metallurgical and Materials Transactions A volume 54, 998–1009, 2023
-
Von der Laserbeschriftung bis zum Lasermaterialabtrag, Springer Vieweg, Wiesbaden, 2023DOI
Kollbach, Ch.; Wilhelm, H.; Hartl, Ch.
-
Mechanics of hydroforming. In: Mechanics of materials in modern manufacturing methods and processing techniques, V.V. Silberschmidt (editor), Elsevier, Amsterdam, NL, 71-109
Hartl, Ch., 2020
-
Hydroforming. In: Modern Manufacturing Processes, M. Koc, T. Özel (editors), John Wiley & Sons, Hoboken, USA,15-45
Hartl, Ch., 2019
-
Review on Advances in Metal Micro-Tube FormingDOI
Hartl, Ch., 2019
Metals 2019, 9(5), 542 -
Fabrication of Polymeric Micro-Tube Components - Recent Developments. Proceedings of the Institute of Vehicles 4 (122), 33–43.DOI
Hartl, Ch.; Anyasodor, G., 2019
-
Hartl, Ch.; Radetzky, M.: Simulation-based thermomechanical stress analysis of forming tools in hot profile rolling processes.
Hartl, Ch.; Radetzky, M., 2018
Proc. of the XXIXth German Polish Scientific Seminar Development Trends in Design of Machines and Vehicles, Cologne 15.-17. May 2018, ed. R. Haas, Scientific Reports of the Cologne University of Applied Sciences -
Reliability in Micro-Manufacturing - Case Studies and Optimization Strategies. Proceedings of the Institute of Vehicles 3 (112), S. 83-92
Hartl, Ch; Chlynin, A., 2017
-
Challenges, trends and approaches of future reliability engineering in high precision manufacturing. In Proceedings of 24th International Conference on Production Research, ICPR 2017, Poznan, Poland, 30th July - 3rd August 2017, S. 19-24
Bracke, S.; Backes, B.; Patelli, E.; Inoue, M.; Yamada, S.; Ulutas, B.; Hartl, Ch.; Dültgen, P.; Mlynczak, M.; Suer, G., 2017
-
Reliability engineering on face of shorten product life cycles: Challenges, technique trends and method approaches to ensure reliability. Proc. of Conf. European Safety and Reliability, Glasgow, 25. - 29. September 2016
Bracke, S.; Hinz, M.; Inoue, M.; Pateli, E.; Kutz, S.; Gottschalk, H.; Ulutas, B.; Hartl, Ch.; Mörs, P.; Bonnaud, P., 2016
-
Investigations into Forming Limits and Process Control of Micro-Hydroforming (Key note speech). 7th International Conference on Tube Hydroforming, Xi'an, China, 9. - 11. September 2015, 3-16
Hartl, Ch.; Chlynin, A.; Radetzky, M., 2015
-
Micro-hydroforming. In: Micro Manufacturing Engineering and Technology, editor Yi Qin, second edition, Elsevier, Oxford, 323-345
Hartl, Ch., 2015
-
Forming of polymeric tubular micro-components. In: Micro Manufacturing Engineering and Technology, editor Yi Qin, second edition, Elsevier, Oxford, 179-200
Qin, Y.; Zhao, J.; Anyasodor, G.; Hansen, K. S.; Calderon, I.; Konrad, K.; Hartl, Ch.; Arentoft, M.; Chronakis, I. S., 2015
-
The influence of axial compressive stresses on the formability and scattering of process parameters in micro-hydroforming processes of tubes. 4th International Conference on New Forming Technology, Glasgow, UK, 6. - 9. August 2015, 06001-p1-p7.
Hartl, Ch.; Chlynin, A.; Radetzky, M., 2015
-
Evaluation of experimental and numerical investigations into micro-hydroforming of platinum tubes for industrial application. Manufacturing Review 1 (2014) 17, DOI: 10.1051/mfreview/2014015DOI
Hartl, Ch.; Schiefer, H.; Chlynin, A., 2014
-
Prediction accuracy of failure criteria in FE-analyses of hydroforming processes. Machine Dynamics Research 38 (2014) 4, 69-77
Hartl, Ch.; Radetzky, M., 2014
Mitgliedschaften
-
International Journal of Lightweight Materials and Manufacture, Editorial Board Member since 2018IJLMM
-
Aeronautical Manufacturing Technology Magazine, Editorial Board Member since 2017AMTE
-
Manufacturing Review, Associate Editor since 2016Manufacturing Review
-
Association for Vocational Training in Engineering and Science e.V. (Gesellschaft für technisch-wissenschaftliche Fortbildung e.V.), Cologne, Germany, President since 2006
-
VDI Association of German Engineers, Member since 2004VDI
-
Institute of Production Engineering and Organisation GmbH (Institut für Produktionstechnik und –organisation GmbH), Cologne, Germany, Managing Director since 2002IPTO