Dissertation: Datengetriebene Produktion optimieren
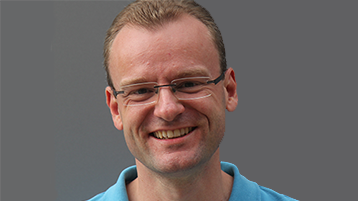
In seiner Dissertation „Automatic Online Algorithm Selection for Optimization in Cyber-Physical Production Systems“ hat Andreas Fischbach untersucht, wie Algorithmen zur Steuerung industrieller Fertigungsprozesse schneller angepasst werden können. Die kooperative Promotion wurde von Prof. Dr. Günter Rudolph (TU Dortmund) und von Prof. Dr. Thomas Bartz-Beielstein (TH Köln) betreut.
Wie erklären Sie Ihr Thema Ihren Nachbarn?
Fertigungsprozesse in der Industrie werden durch viele Parameter wie Drücke, Temperaturen oder Geschwindigkeiten gesteuert. Um diese Vorgänge effizienter zu gestalten, müssen mehrere Einflussgrößen optimiert werden. Hierzu zählen beispielsweise der Durchsatz – die maximale Rate, mit der etwas pro Zeiteinheit verarbeitet werden kann – sowie Energieverbrauch und Ausschuss, also die Fehlproduktion. In modernen Anlagen übernehmen häufig Algorithmen diese Aufgabe. Deren Auswahl hängt wesentlich von der Art des Problems und dem Optimierungsziel ab und erfolgt meist aufwändig manuell. Da industrielle Produktionsverfahren heutzutage häufiger an aktuelle Marktbedürfnisse angepasst werden, müssen sich auch die Algorithmen schneller verändern. Ich habe untersucht, wie dies (teil-)automatisiert umgesetzt werden kann.
Was haben Sie herausgefunden?
Zum einen habe ich einen Algorithmus entwickelt, der datengetrieben den effizientesten Optimierer für einen neu aufgesetzten Fertigungsprozess auswählt. Als Optimierer kommen etwa Evolutionäre Algorithmen zum Einsatz. Diese basieren auf Ideen der biologischen Evolution und entwickeln eine „Population“ von Lösungen kontinuierlich weiter. Eine Lösung entspricht dabei einer Parametereinstellung des Fertigungsprozesses, zum Beispiel die Geschwindigkeit der Verarbeitungszyklen, den wir verbessern möchten. Dies geschieht durch Kreuzung und Mutation. Dabei müssen Suchkriterien wie die Populationsgröße und die Kreuzungs- und Mutationswahrscheinlichkeit für die Optimierung des vorliegenden Fertigungsprozesses möglichst passend gewählt werden.
Zum anderen habe ich einen flexiblen Bauplan für eine Software entworfen. In dieser sogenannten Software-Architektur werden etwa Daten für die Steuerung von Anlagen gespeichert. Ebenfalls können neue Maschinen und Anwendungsfälle hinzugefügt werden. Alle Informationen fließen bildlich gesprochen in einer Pipeline zusammen und am Ende kommt die Software heraus. Unser Prototyp konnte bei einer Spritzgießmaschine, die zur Herstellung von Kunststoffprodukten wie Autoteilen oder Verpackungen eingesetzt wird, die Qualität der hergestellten Teile und die Verarbeitungszeit optimieren.
Was begeistert Sie an Ihrem Thema?
Der Einsatz von Verfahren, die die Wirtschaftlichkeit und Nachhaltigkeit eines Fertigungsprozesses erhalten oder verbessern, ist für Unternehmen von enormer Bedeutung, um wettbewerbsfähig zu bleiben. An einem Projekt zu arbeiten, dessen Ergebnisse direkt in der industriellen Praxis eingesetzt werden können, ist für mich die größte Motivation.
Wie kann es mit Ihren Ergebnissen weitergehen?
Die Ergebnisse können als Grundlage dienen, um neben den untersuchten Produktionsschritten auch andere Anwendungsfälle wie zum Beispiel die datengetriebene Zustandsüberwachung von Anlagen oder die vorausschauende Wartung in den Blick zu nehmen. Ziel wäre es, die Erkenntnisse in eine mit geringem Aufwand anpassbare Lösung zu überführen.
August 2023