Modellfabrik
In der Modellfabrik werden Pumpen und Hydro-Zahnradmotoren produziert, wie sie von renommierten deutschen Qualitätsunternehmen ebenfalls hergestellt werden. Zum Produktionsspektrum der Modellfabrik gehören Schwenkflügelvakuumpumpen, Schlauchpumpen, Kraftstoffpumpen sowie Hydro-Zahnradmotoren, die teilweise in verschiedenen Varianten produziert werden.
Wissensvermittlung findet oft recht theoretisch statt, sodass nicht selten nur wenige oder keine Bezüge zur industriellen Praxis hergestellt werden. In dieser Lernfabrik hingegen können Strukturen und Abläufe erprobt und nach aktuellen betriebswirtschaftlich-organisatorischen sowie logistischen Prinzipien optimiert werden. Sowohl Studierende der TH Köln als auch Mitarbeiterinnen und Mitarbeiter aus Industrieunternehmen können in der Modellfabrik erleben, wie Probleme in der Praxis identifiziert und analysiert werden. Zudem kann vermittelt werden, welche Schritte notwendig sind, um effizient zu Lösungen zu kommen, die die Ideen aller Beteiligten berücksichtigen. Dadurch können die Schulungsteilnehmerinnen und -teilnehmer praxisnah Erfahrungen sammeln, ihre theoretischen Kenntnisse anwenden und sich neue Kenntnisse aneignen. Praxisnahes Lernen und Teamarbeit werden in der Modellfabrik in ein durchgängiges pädagogisches Gesamtkonzept integriert.
Durch die Einbeziehung der Modellfabrik in Lehre und Weiterbildung kann theoretisches Wissen praxisnah angewendet werden. So können Studierende, Mitarbeiterinnen und Mitarbeiter sowie Führungskräfte lernen, wie Teile für echte Pumpen und Hydro-Zahnradmotoren beschafft, gefertigt und montiert werden. Außerdem können sie lernen, wie die logistischen Zusammenhänge hinsichtlich effizienter Informations- und Materialflüsse gestaltet werden sollten. Die Vermeidung von Fehlern durch Anwendung des Poka Yoke-Prinzips ist dabei von grundlegender Bedeutung.
Die Studierenden sowie Mitarbeiterinnen und Mitarbeiter aus Unternehmen lernen, den Herstellungsprozess von Pumpen und Hydrozahnradmotoren unter betriebswirtschaftlich-organisatorischen und logistischen Gesichtspunkten zu optimieren.
Geht man „rückwärts“ vom Kunden aus gesehen durch die Fabrik, so verfügt sie über einen Versandbereich, eine Qualitätssicherung, einen Montagebereich, ein Hochregallager, einen Faserlaser, eine CNC-Drehmaschine, eine Horizontalbandsäge und einen Fertigungsleitstand (Abbildungen 1 und 2 geben einen Überblick).
Prozessschritte in der Modellfabrik
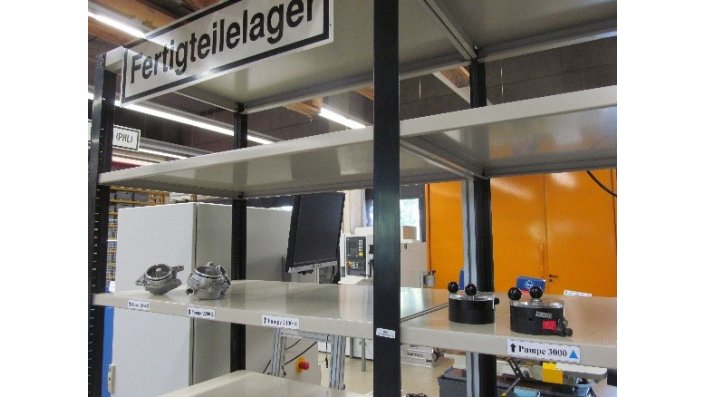
Im Versandbereich werden die fertigen Pumpen und Hydro-Zahnradmotoren nach ihrer Fertigstellung für den Versand zu den Kunden bereitgestellt. (Bild: TH Köln)
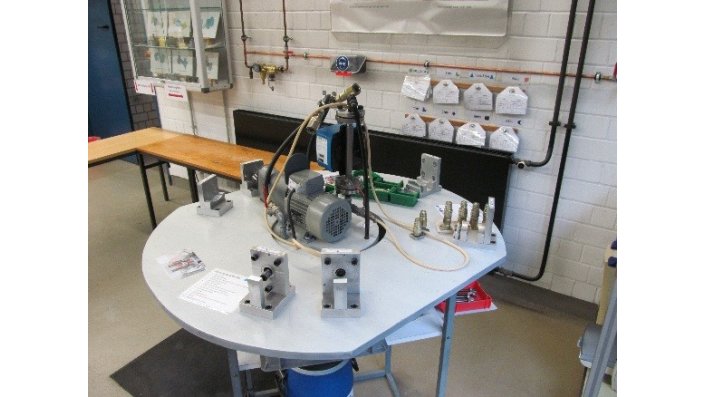
Die davor angeordnete Qualitätssicherung stellt einen den Kundenwünschen entsprechenden hohen Qualitätsstandard sicher. Mit einem Durchflussprüfer werden bei Pumpen und Hydro-Zahnradmotoren die Qualitätsparameter Funktionsfähigkeit, Dichtigkeit und Durchflussmenge geprüft. (Bild: TH Köln)
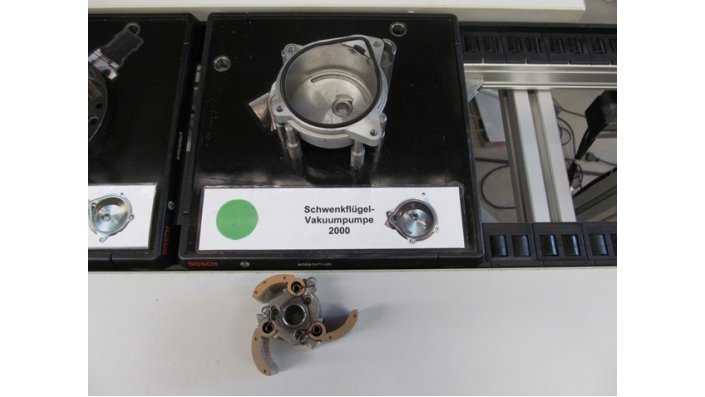
In der Montage werden Pumpen und Hydro- Zahnradmotoren aus eigengefertigten und fremdbezogenen Komponenten zusammengebaut. Anhand von Explosionszeichnungen und bebilderten Montageanleitungen werden die Pumpen und Hydro-Zahnradmotoren auf speziellen Montagevorrichtungen mit einem Druckluft-Schrauber montiert. Die Visualisierung der benötigten Teile in der Arbeitsanleitung sowie auf den Kisten vereinfacht den Montageprozess und hilft Montagefehler zu vermeiden. (Bild: TH Köln)
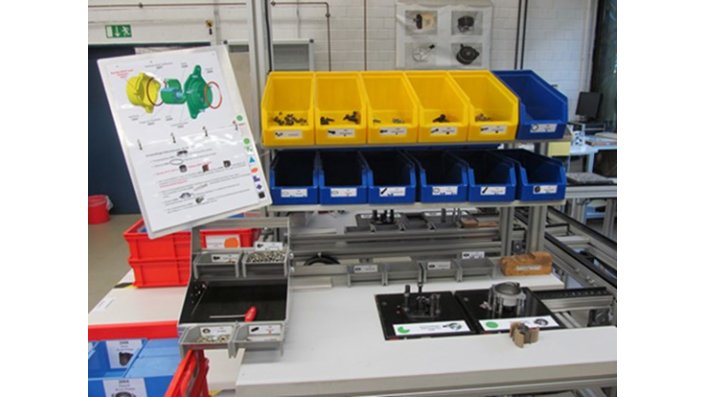
Im Montagebereich werden A- und B-Teile kundenauftragsindividuell bereitgestellt. Die Bereitstellung der C-Teile hingegen erfolgt kundenauftrags-neutral als Schüttgut in schräg angeordneten Kisten. (Bild: TH Köln)
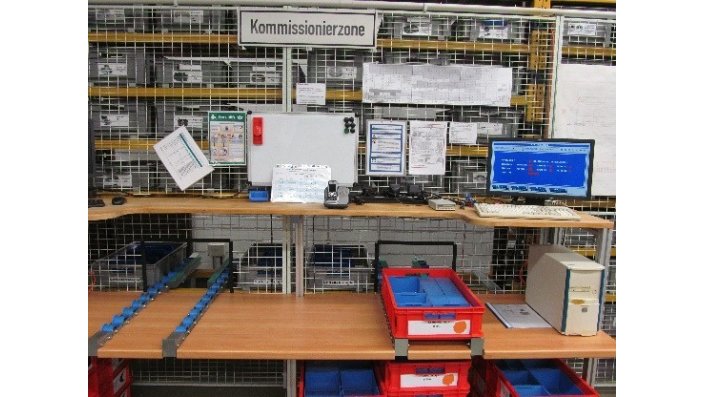
Im Hochregallager stehen sowohl eigengefertigte als auch fremdbezogene Bauteile und Baugruppen zur Verfügung. Sie werden ein- und ausgelagert und entsprechend der Produktionsaufträge kommissioniert. In der Kommissionierung werden die Einzelteile den Aufträgen entsprechend zusammengestellt und anschließend zur Montage gebracht. Durch eine Poka-Yoke-Tastatur zur Fehlervermeidung wird sichergestellt, dass physische Ein- und Auslagerung sowie die EDV-technische Abwicklung sinnvoll koordiniert und Fehler systematisch vermieden werden. (Bild: TH Köln)
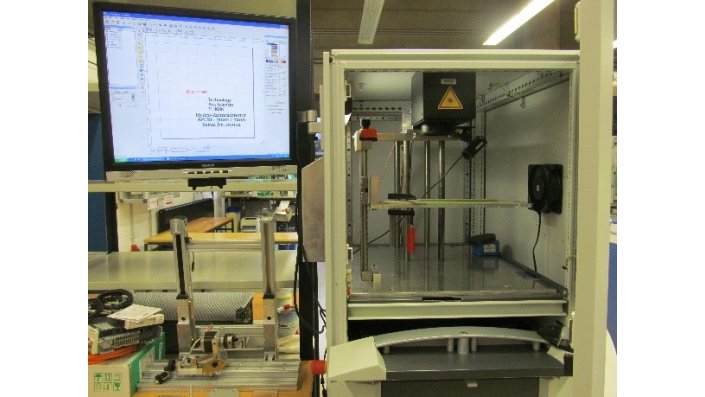
Mit dem Faserlaser können die Produkte kundenindividuell beschriftet und logistische Kennzeichnungen vorgenommen werden. Der Faserlaser arbeitet mit einer maximalen optischen Ausgangsleistung von 11,1 Watt und einem minimalen Fokusdurchmesser von 35 µm (Laserfokus) bei einem Abstand zwischen Linse und Fokus von 160 mm. Der Arbeitsbereich liegt zwischen 100x100 mm bis 110x110 mm. (Bild: TH Köln)
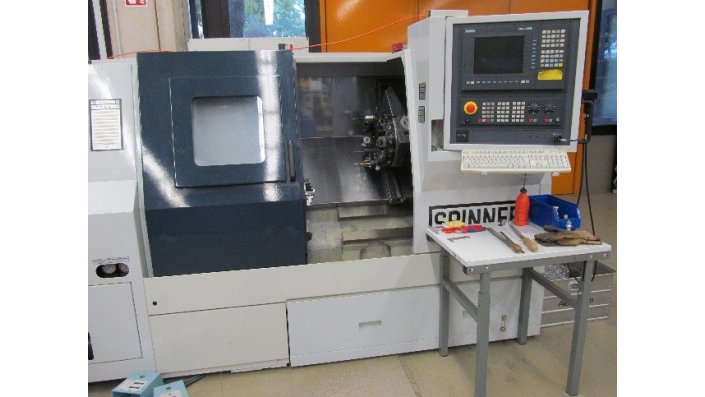
Auf der CNC-Drehmaschine werden die Aluminium-Wellen für die Schwenkflügel-Vakuumpumpen hergestellt. (Bild: TH Köln)
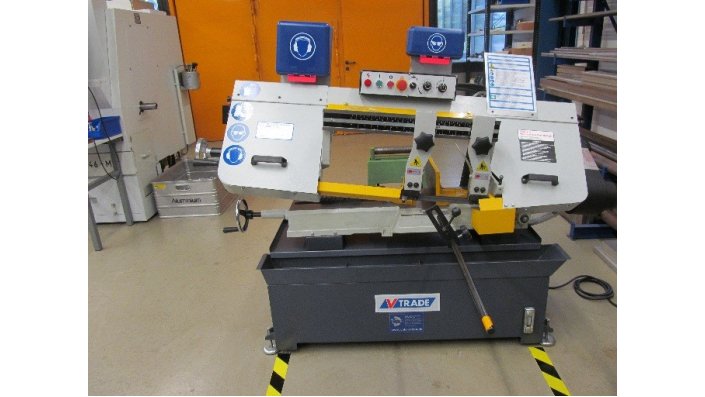
Mit der Horizontalbandsäge werden Pumpenwellen aus Rundprofilen und Pumpendeckel aus Vierkantprofilen gesägt. (Bild: TH Köln)
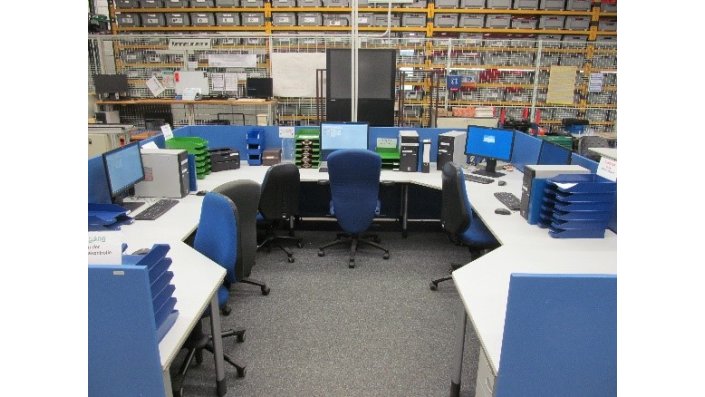
Der Leitstand übernimmt die administrativen Tätigkeiten in der Modellfabrik. Hier werden Kundenaufträge angenommen, Produktionsaufträge generiert und das Produktionsprogramm geplant und gesteuert. Zudem hat der Leitstand die Aufgabe, Materialbestellungen durchzuführen. Die Qualitätssicherung gibt zudem Rückmeldungen an den Leitstand. (Bild: TH Köln)
Lehre in der Modellfabrik
Bei Schulungen in der Modellfabrik können den Teilnehmerinnen und Teilnehmern (also Studierenden sowie Mitarbeiterinnen und Mitarbeitern aus Unternehmen) logistische Zusammenhänge zwischen unterschiedlichen betrieblichen Funktionen vermittelt werden. Durch Job Rotation wird ihnen ermöglicht, eine praxisnahe Einsicht in die verschiedenen Funktionen eines Produktionsunternehmens zu erhalten. Alternativ können Teilnehmerinnen und Teilnehmer auch Lernkurveneffekte erfahren, indem sie bei den Produktionsdurchläufen jeweils auf ihren Arbeitsplätzen bleiben. Dabei merken Sie, wie sie durch immer mehr Übung zunehmend ihre Leistung (beispielsweise die Ausbringungsmenge und die Qualität) verbessern.
Im Rahmen des Studiums wird die Modellfabrik primär dazu genutzt Rationalisierungspotenziale im Sinne einer LEAN Produktion zu erkennen und zu erschließen. Hierzu werden die auch in der Unternehmenspraxis üblichen Vorgehensweisen eingesetzt. Die bisherigen Themenschwerpunkte weisen eine breite Vielfalt auf und reichen von ‚Rationalisierung der Modellfabrik’, ‚Grüne Modellfabrik’, Automatisierung in der Modellfabrik’, ‚Flexibilität und Wirtschaftlichkeit in der Modellfabrik’ sowie ‚Industrie 4.0 in der Modellfabrik’ bis hin zum Schwerpunkt ‚Sicherheit in der Modellfabrik’. Zu diesen Themen wurden bereits Projektarbeiten verfasst und die erarbeiteten Lösungen wurden mit kleinen dreidimensionalen Modellen visualisiert.
Die Erarbeitung der Themen erfolgte dabei in drei aufeinanderfolgenden Schritten:
- IST-Analyse zur Identifikation der wesentlichen Verbesserungspotenziale,
- SOLL-Konzept zur Verdeutlichung der Optimierungsansätze
und schließlich
- Maßnahmenplan-Erstellung mit Abschätzung der erforderlichen personellen, zeitlichen und finanziellen Ressourcen.
Durch Anwendung dieser Vorgehensweise lernen Studierende und andere Teilnehmerinnen und Teilnehmer der Schulungen die wichtigsten relevanten Prozesse eines Produktionsbetriebs systematisch zu analysieren und gezielt zu optimieren. Die praxisorientierte Bearbeitung der Problemstellungen in Gruppen fördert zudem die Teamfähigkeit. Bei allen praktischen Tätigkeiten in der Modellfabrik wird auch großer Wert darauf gelegt, beim logistischen Projektmanagement eine klare Fokussierung auf die optimale Erfüllung von Kundenwünschen in den Vordergrund zu stellen.