Duro:Net
Transfer Moulding von Duroplasten mit Hilfe künstlicher neuronaler Netze
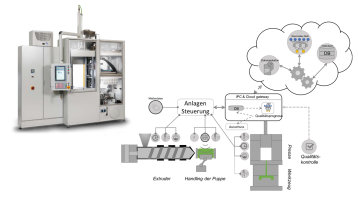
- Einsparung von Einrichtzeit und Materialkosten
- Sicherung einer hohen Qualität der Plastifizierung von schwankenden Materialchargen
- Selbstständige Optimierung der Prozessparameter eines Plastifizierers
Kurzfassung der Projektbeschreibung:
Aufgrund des immer größer werdenden Absatzmarktes für Elektroautos und der zunehmenden Mechatronisierung von Fahrzeugen werden vermehrt Elektronikkomponenten benötigt, die gegenüber der Einsatzumgebung eine hohe thermische und chemische Belastungsgrenze haben und eine hohe Schlagfestigkeit besitzen.
Kunststoffbauteile aus Duroplasten erfüllen diese Anforderungen, weshalb ein hohes wirtschaftliches Potential in duroplastischen Erzeugnissen liegt. Dies betrifft zum Beispiel mechatronische Komponenten, die im Getriebe verbaut sind.
Eine weitere weitverbreitete Kunststoffart sind die Thermoplaste. Diese sind duroplastische Kunststoffe, jedoch aufgrund der Materialeigenschaften unter anderem in den Bereichen Widerstandsfähigkeit und Temperaturbeständigkeit deutlich unterlegen. Lediglich Hochleistungsthermoplaste besitzen mit Duroplasten vergleichbare Eigenschaften. Da Hochleitungsthermoplaste teurer in der Anschaffung und Verarbeitung sind und somit meist unwirtschaftlicher, werden Duroplaste für die genannten Anwendungsfälle in der Industrie verarbeitet.
Duroplastprodukte haben derzeit ein großes wirtschaftliches Potential und Maschinen zur Verarbeitung von Duroplasten sind mehr denn je gefragt.
Transfer Moulding (Spritzpressen) ist das gebräuchlichste Verfahren für die Umhüllung von Elektrobauteilen, da die Prozessdrücke im Gegensatz zum Spritzgießverfahren weitaus geringer sind und somit die empfindlichen Elektronikbauteile nicht beschädigt werden.
Die Boyke Technology vertreibt Sondermaschinen, die die Duroplastverarbeitung in einem zweistufigen Prozess ermöglichen. In diesem Verfahren wird zunächst ein Vorformling (Puppe) vorplastifiziert und anschließend in einer Presse verarbeitet. Der Duroplast reagiert in der Presse und vernetzt sich, sodass eine formstabile Hülle entsteht. Die Komplexität der physikalischen Zusammenhänge, die während der Verarbeitung von Duroplasten mittels Spritzpressen im Zylinder herrschen, stellen die größte Problematik bezüglich der Produktqualität dar. Die Materialeigenschaften von Duroplasten schwanken jedoch von Charge zu Charge, so dass zusätzliche Prozessunsicherheiten bei der Verarbeitung auftreten.
Dies hat zur Folge, dass bei der Verarbeitung von Duroplast Kunststoffen mittels Spritzpressen Kosten- und Materialintensive Rüstprozesse entstehen.
In diesem Projekt wird eine Inline-Messsystem realisiert. Diese Entwicklung ist der erste Schritt einer Optimierungsstrategie für das Transfer Moulding. Besonders kleine und mittlere Unternehmen (KMU), welche die Hauptkundengruppe sind, profitieren von der prozessoptimierten Transfer Moulding Anlage der Fa. Boyke, da diese einen sicheren und stabilen Verarbeitungsprozess für kostengünstige Kleinserien realisieren können.
Auf einen Blick
Kategorie | Beschreibung |
---|---|
Forschungsprojekt | Duro:Net - Transfer Moulding von Duroplasten mit Hilfe künstlicher neuronaler Netze |
Leitung | Prof. Dr.-Ing. Ulf Müller zur Personenseite |
Fakultät | Fakultät für Anlagen, Energie- und Maschinensysteme |
Institut | Institut für Produktentwicklung und Konstruktionstechnik |
Projektpartner | Boyke Technology GmbH Mehr |
Fördermittelgeber | Zentrales Innovationsprogramm Mittelstand (ZIM) des Bundesministeriums für Wirtschaft und Energie (BMWi) |
Laufzeit | 06 / 2018 - 04 / 2020 |